Stainless Steel
Metallographic Preparation Solutions by Material
Use this guide for advice on how to start performing metallographic preparation and analysis on stainless steel. Included are tips for achieving the best results for your metallographic application.
Things to consider when working with stainless steel
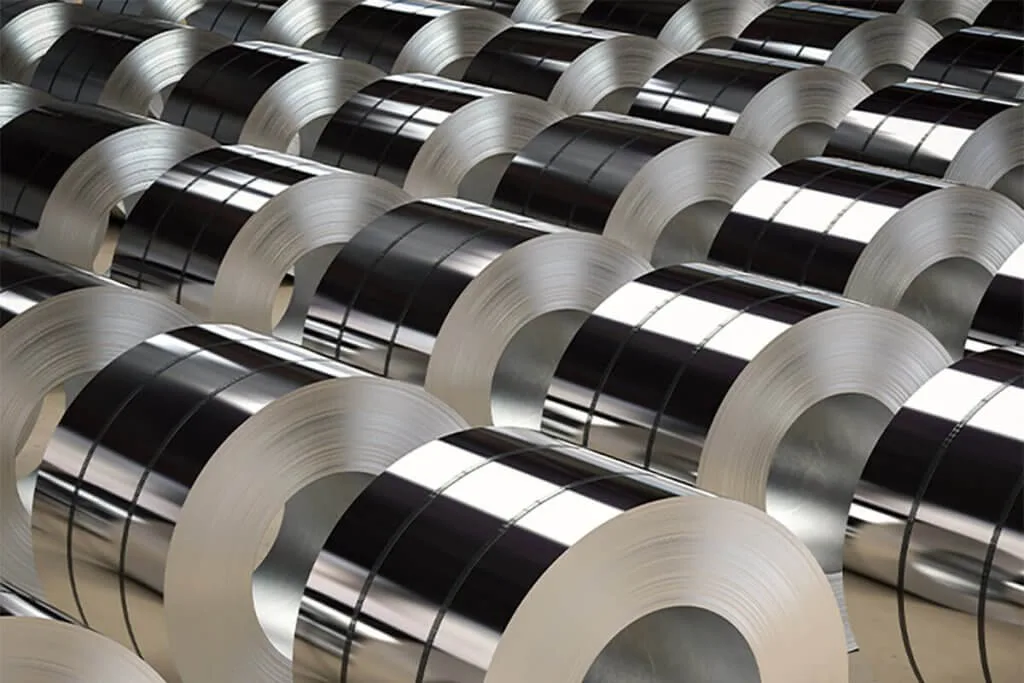
Ferrous materials are widely used in many different industries due to their versatility. Properties can vary depending on slight changes in composition and processing steps. Excellent surface finish is generally straightforward using one of the procedures below.
Stainless Steel Cutting Tips
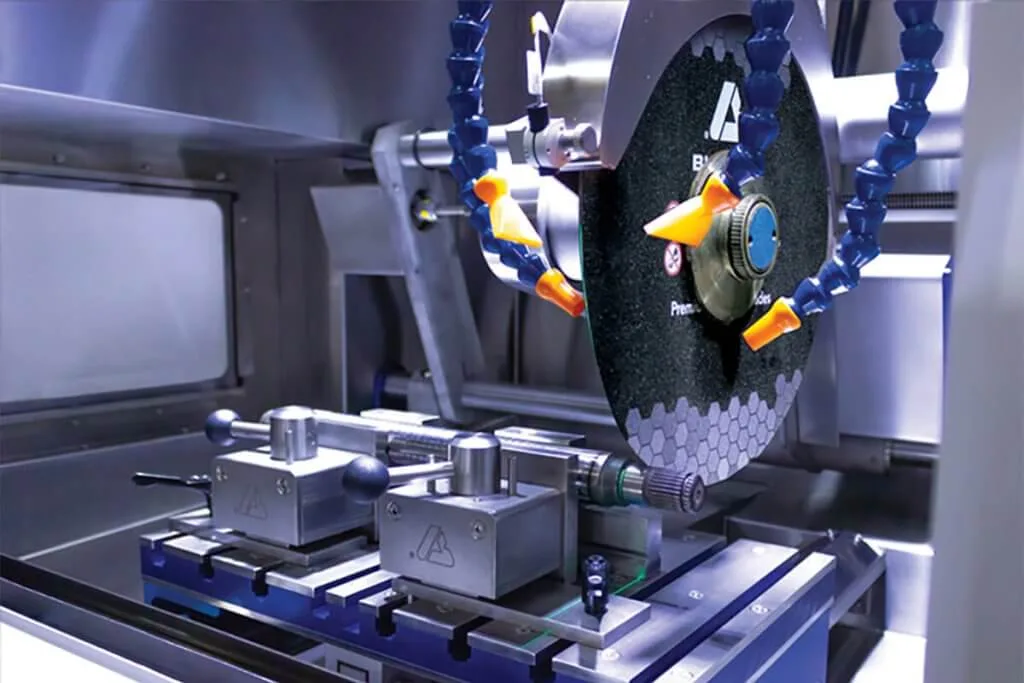
All sectioning should be performed wet, with an ample flow of coolant directed into the cut. Wet cutting will produce a smoother surface finish than a dry cut. Using coolant will also guard against surface damage caused by overheating and mechanical strains. Reducing damage while sectioning is important. Mechanical damage can penetrate deep into the structure, this can be difficult to remove in later preparation steps. There are two main types of cutting tools offered: Abrasive and Precision saws.
Abrasive Cutting Tips
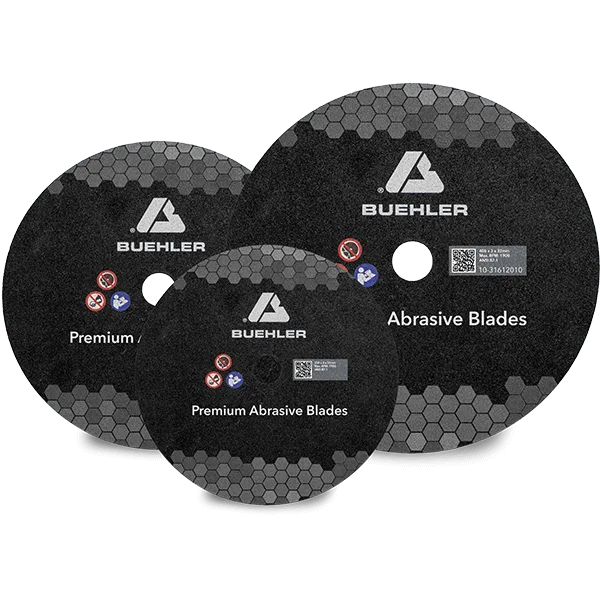
Abrasive blades have different bond strengths and are recommended based on the efficiency of their bond strength and abrasive type with different materials. Choosing an incorrect blade can lead to an improper wear rate and thermal damage, possibly altering the microstructure. An abrasive blade is entirely made up of abrasive that is bound together by resin. When used, blades get smaller in size until they can no longer cut. A new blade can then be put on the sectioning piece of equipment to make additional cuts.
Abrasive wheels/blades should be selected according to the material type and size of the part being cut. When cutting ferrous materials, knowing the hardness of your material can help narrow down the blade to select. In some instances, like Buehler’s, blades are grouped by the material hardness. Generally the harder the steel the softer the blade bond, this ensures that worn abrasive is broken away and fresh abrasive is revealed to continue efficient sectioning. Softer steel can be cut with a harder bond blade which lends itself to extended blade life.
The size of the abrasive blade also affects cutting parameters. Larger, thicker blades remove more material but also generate more heat than a thinner blade. To reduce the heat produced by blades the feed rates should be lowered.
Recommended abrasive blade for ferrous materials | ||||
---|---|---|---|---|
Diameter | 10in (254mm) | 12in (305 mm) | 14in (356mm) | 16in (406mm) |
HRC 15-35 | 102511P 0.06in [1.5mm] | 103011P 0.079in [2mm] | 12-4305-010 0.063in [1.6mm] | |
HRC 35-50 | 102510P 0.06in [1.5mm] | 103010P 0.083in [2.mm] | 1103510P 0.098in [2.5mm] | 10-31616-010 0.125in [3mm] |
HRC 50-60 | 10-31014-010 0.06in [1.5mm] | 10-31212-010 0.08in [2mm] | 103509P 0.098in [2.5mm] | 10-31612-010 0.125in [3mm] |
HRC 60+ | 102509P 0.06in [1.5mm] | 103009P 0.08in [2mm] | 103509P 0.098in [2.5mm] | 10-31610-010 0.125in [3mm] |
High Speed Steel, Stainless Steel, Carburized Steel | 102508P 0.063in [1.6mm] | 103008P 0.079in [2mm] | 103508P 0.102in [2.6mm] | |
General Steel, Superalloys, Non-ferrous | 12-4205-010 0.051in [1.3mm] | 12-4405-010 0.055in [1.4mm] | 12-4305-010 0.063in [1.6mm] | 12-5605-010 0.075in [1.9mm] |
Precision Cutting Tips
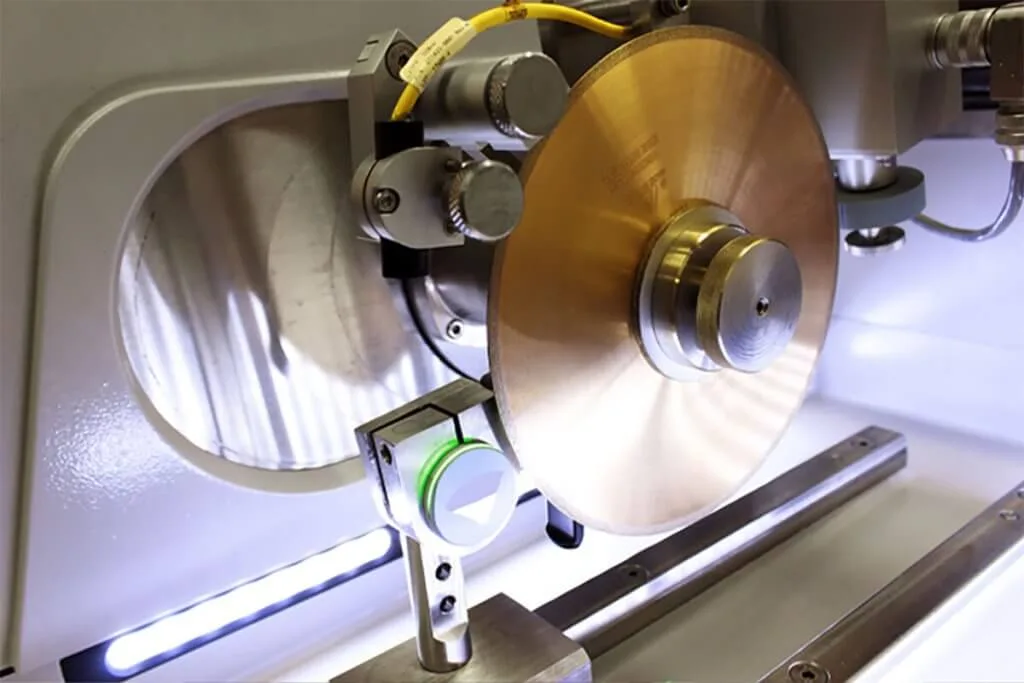
Precision cutters are used in metallographic preparation of ferrous materials when cutting samples that are small or delicate. Precision blades don’t break down as they are being used. On the outer edge of the blade there is a section where abrasive has been bonded with metal alloy and if taken care of one wafering blade can outlast a box of abrasive blades. Wafering blades can be used with ferrous material for more difficult cuts including making a precise cut close to a feature of interest, or when it is critical to reduce the width of a cut (kerf loss).
An additional benefit of using a precision cutter is a lower load is applied and consequently less heat is generated, reducing the amount of damage.
Abrasive blades are also made for precision cutters. They can be used when potential for blades breaking is high. This could be if you have a difficult to clamp part, have a part that might shift during sectioning or you have more variability in the process (ex: multiple operators).
Recommended precision blades for Stainless Steels | ||||
---|---|---|---|---|
Blade Type | 5in (127mm) | 7in (178mm) | 8in (203mm) | Dressing Stick |
Precision Blades | 11-5265 0.020in [0.4mm] | 11-5267 0.025in [0.6mm] | 11-5268 0.035in [0.9mm] |
11-1190
11-2490 |
Abrasive Blades | 10-4061-101 0.019in [0.48mm] | 11-4207-010 0.030in [0.76mm] |
Stainless Steel Mounting Tips
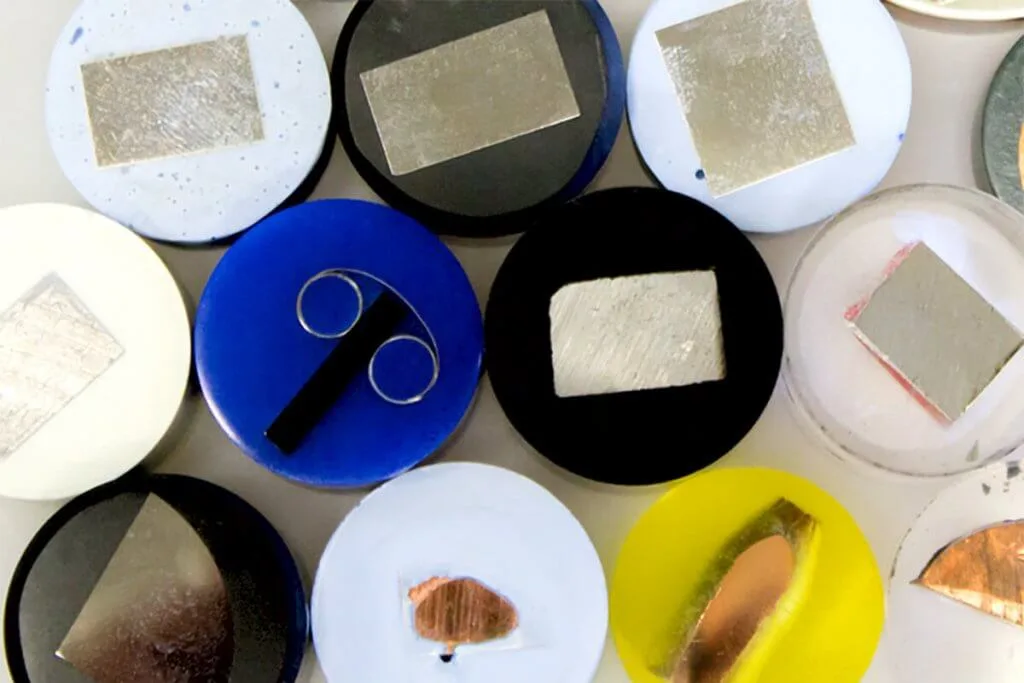
Mounting metallographic samples can allow automation and increase ease of handling during the subsequent steps of metallographic preparation and examination. Intricately shaped samples can be mounted to create uniform shapes allowing automation of the sample preparation process.
Mounting samples also protects and preserves edges or surface defects during metallographic preparation. The method of mounting should in no way alter the microstructure of the specimen. Pressure and heat are the most common sources of injurious effects. Temperatures around 350oF and pressures around 4000 PSI are common for hot compression mounting.
Sample geometry and properties can determine the appropriate method for mounting ferrous samples. Use castable mounting when samples are thin or deformed easily. Samples such as these tend to be sensitive to high pressures. If samples are not sensitive to pressure hot compression mounting can be a time and money saver.
For electron microscopy, ProbeMet is a suitable copper-based conductive media. If copper content is of interest in the sample KonductoMet® is a carbon-filled conductive alternative to ProbeMet.
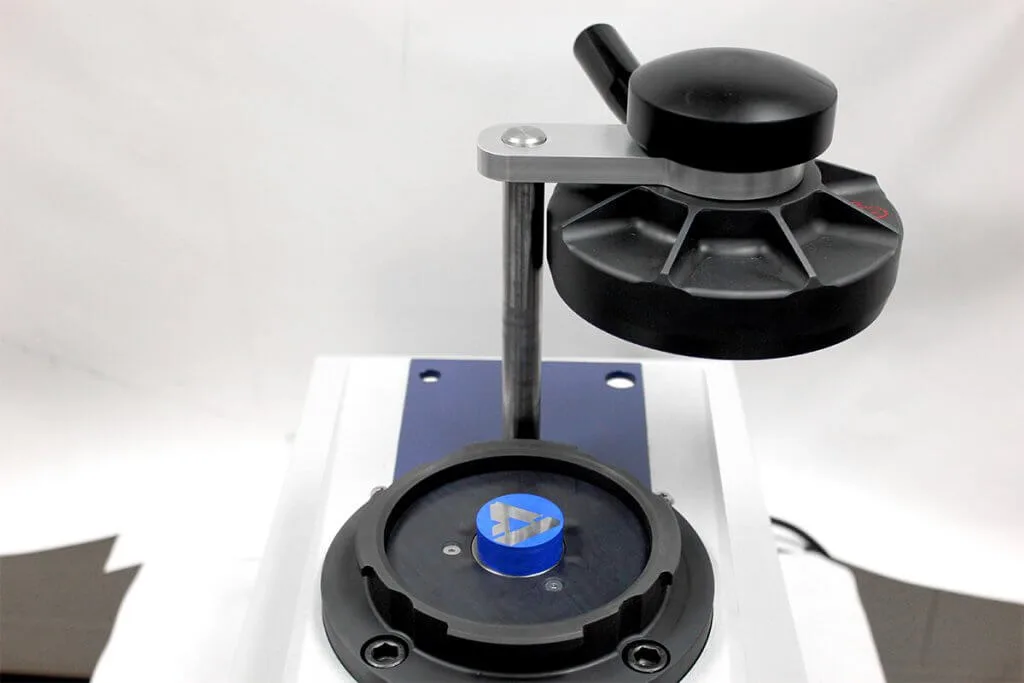
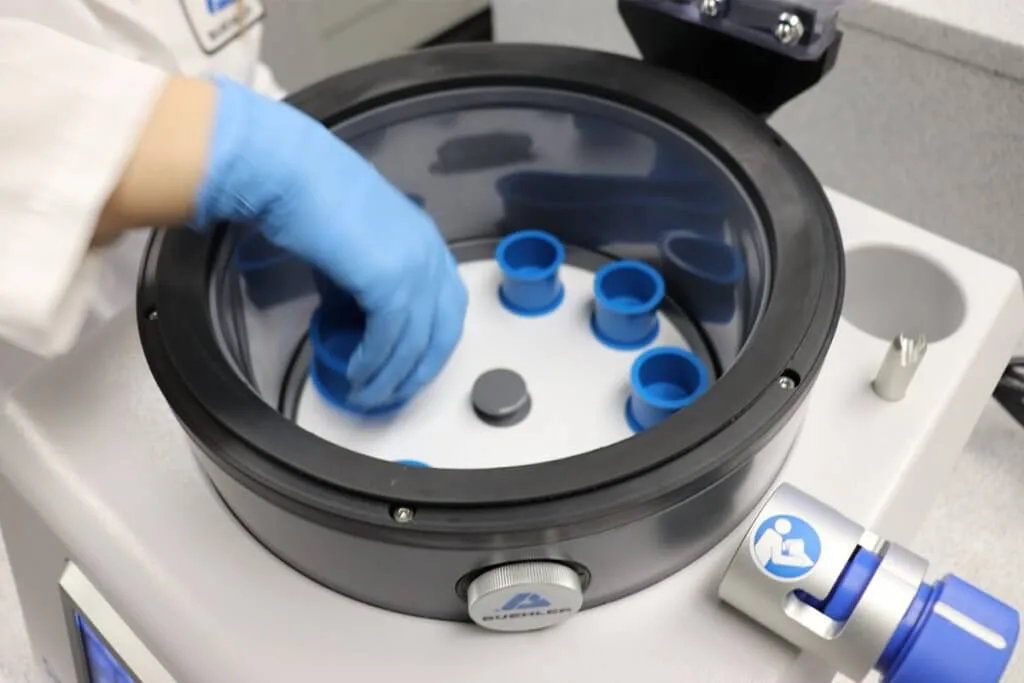
Careful selection can ensure media meets mounting needs regarding timing, viscosity, temperature, and shrinkage. Acrylic systems can increase throughput due to the quick curing time of 30 minutes or less. Though quicker in curing, sample adhesion and viscosity of acrylics can sometimes be lacking especially with more intricate shapes. This is where epoxy systems can help. With longer working times mixed epoxy can be used with a vacuum system to help penetration levels in intricate geometries.
Stainless Steel Grinding & Polishing Tips for All Methods
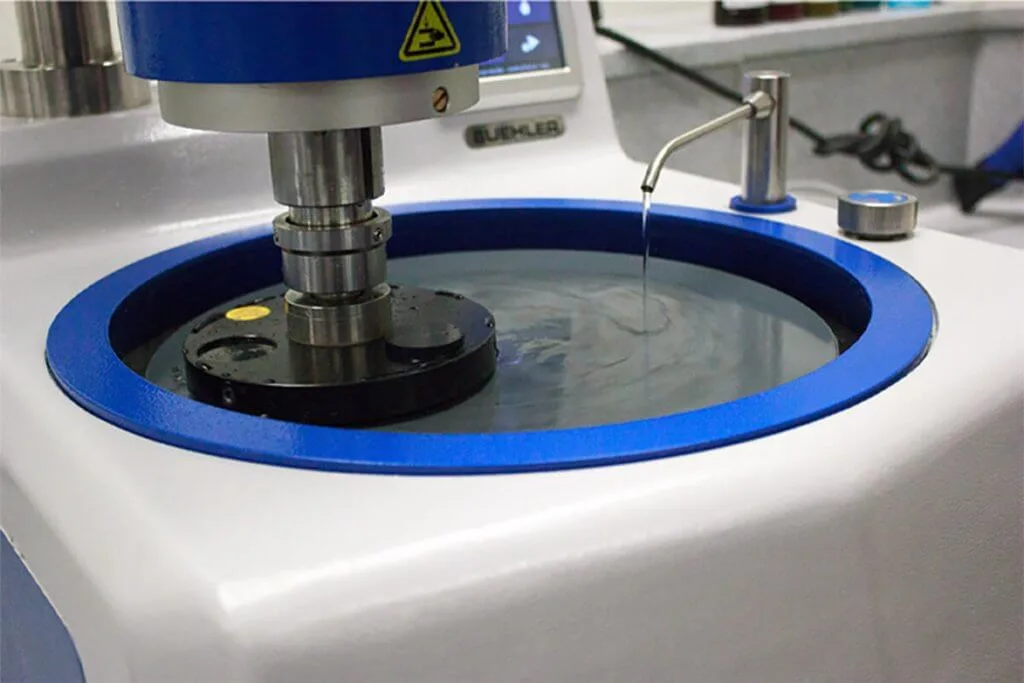
Hard steels are usually not as challenging to prepare as soft steels. Some harder alloys can sometimes be prepared with a three-step method.
Pure iron, and austenitic stainless steels are hard to prepare without scratches or deformation. After mechanical grinding and polishing a vibratory step using a napped cloth with MasterPrep® can improve surface finish.
For ferritic stainless grades, solution annealed austenitic grades and annealed maraging grades Hercules S discs or UltraPol with a 30-μm suspension can be used for the first step. If in the harder range of materials (>50HCR) the suggested 120 grit silicon carbide papers can be used instead. If a better surface finish is needed a 1-μm step with Trident can be added following the 3-μm step or a vibratory step can be added to the end of the sequence.
Using Buehler’s Burst dispensing system can conserve diamonds and improve consistency.
The ideal rate for the Burst dispensing system changes with the size of the platen and the polishing cloth that is being used. As a general guideline, for platen size of 8” a burst setting of 3 is a good starting point, for sizes of 10″ and 12″ set the burst system to 4 and adjust as needed. Some experimentation may be required to determine optimal settings to ensure sufficient abrasive and wetting of the cloth. Burst dispensers are also capable of dispensing extenders simultaneously with diamond, if desired.
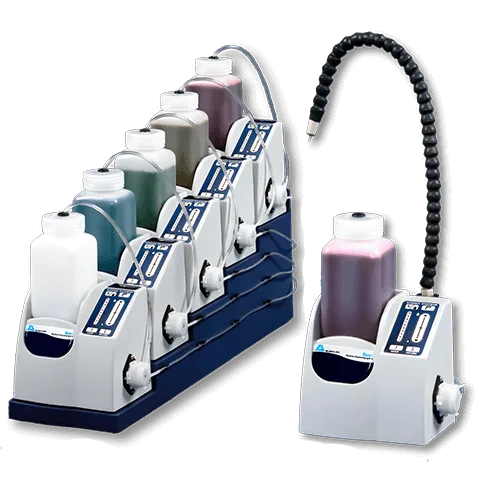
Loads listed in grinding and polishing methods are recommendations for one 1.25″ mounted specimen. If using central force during preparation the force listed should be multiplied by the number of samples being polished. For different sample sizes, use our load conversion calculator to determine the correct load for your application.
Procedure for Grinding and Polishing Stainless and Maraging Steel | ||||
---|---|---|---|---|
Surface | Loads [N] | Base Speed [rpm] | Relative Rotation | Time |
CarbiMet® 120 to 320 grit | 6 [27] | 300 rpm |
![]() | Until Plane |
UltraPad with 9um MetaDi® Supreme Diamond | 6 [27] | 150 rpm |
![]() | 5:00 |
Trident with 3um MetaDi Supreme Diamond | 6 [27] | 150 rpm |
![]() | 3:00 |
ChemoMet® with 0.05um MasterPrep® Alumina | 6 [27] | 150 rpm |
![]() | 2:00 |
![]() ![]() |
Stainless Steel Etching Tips
Table 20.5: Iron and Steel | |
---|---|
Composition | Comments |
90-99mℓ methanol or ethanol 1-10mℓ HNO3 | Nital. Most common etchant for Fe, carbon and alloy steels, cast iron. Reveals alpha grain boundaries and constituents. Excellent for martensitic structures. The 2% solution is most common, 5-10% used for high alloy steels (do not store). Use by immersion or swabbing of sample for up to about 1 minute. |
100mℓ ethanol 4g picric acid | Picral. Recommented for structures consisting of ferrite and carbide. Does not reveal ferrite grain boundaries. Addition of 0.5-1% zephiran chloride improves etch rate and uniformity. |
100mℓ ethanol 5mℓ HCl 1g picric acid | Vilella’s reagent. Good for ferrite-carbide structures. Produces grain contrast for estimating prior austenite grain size. Results best on matentsite tempered at 572-932°F [300-500°C]. Occasionally reveals prior-austenite grain boundaries in high alloys steels. Outlines constituents in stainless steels. Good for tool steels and martensitic stainless steels. |
Saturated aqueous picric acid solution grain plus small amount of a wetting agent | Bechet and Beaujard’s etch, most successful etchant for prior-austenite boundaries. Good for martensitic bainitic steels. Many wetting agents have been used, sodium tridecylbenzene sulfonate is one of the most successful (the dodecyl version is easier to obtain and works as well). Use at 68-212°F [20-100°C]. Swab or immerse sample for 2-60 minutes. Etch in ultrasonic cleaner (see ref. 2, pg 219-223). Additions of 0.5 CuCl2 per 100mℓ solution or about 1% HCl have been used for higher alloy steels to produce etching. Room temperature etching most common. Lightly back polish to remove surface smut. |
150mℓ water 50mℓ HCl 25mℓ HNO3 1g CuCl2 | Modified Fry’s reagent. Used for 18% Ni maraging steels, martensitic and PH stainless steels. |
100mℓ water 25g NaOH 2g picric acid | Alkaline sodium picrate. Best etch for McQuaid-Ehn carburized samples. Darkens cementite. Use boiling for 1-15 minutes or electrolytic at 6 V DC, 0.5 A/in2, 30-120 seconds. May reveal prior-austenite grain boundaries in high carbon steels when no apparent grain boundary film is present. |
3 parts HCl 2 parts glycerol 1 part HNO3 | “Glyceregia.” For austenitic stainless steels. Reveals grain structure, outlines sigma and carbides. Mix fresh, do not store. Use by swabbing. |
100mℓ ethanol 100mℓ HCl 5g CuCl2 | Kalling’s no. 2 (“waterless” Kalling’s) etch for austenitic and duplex stainless steels. Ferrite attacked readily, carbides unattacked, austenite slightly attacked. Use at 68°F [20°C] by immersion or swabbing. Can be stored. |
15mℓ HCl 10mℓ acetic acid 5mℓ HNO3 2 drops glycerol | Acetic glyceregia. Mix fresh, do not store. Use for high alloy stainless steels. |
100mℓ water 10g K2Fe(CN)6 10g KOH or NaOH | Murakami’s reagent. Usually works better on ferritic stainless grades than austenitic grades. Use at 68°F [20°C] for 7-60 seconds: reveals carbides sigma faintly attacked with etching up to 3 minutes. Use at 176°F [80°C] to boiling for 2-60 minutes: carbides dark, sigma blue (not always attacked), ferrite yellow to yellow-brown, austenite unattacked. Do not always get uniform etching. |
100mℓ water 10g oxalic acid | Use for stainless steels at 6 V DC. Carbides reveal by etching for 15-30 seconds, grain boundaries after 45-60 seconds, sigma outlined after 6 seconds. 1-3 V also used. Dissolves carbides, sigma strongly attacked, austenite moderately attacked, ferrite unattacked. |
100mℓ water 20g NaOH | Used to color ferrite in martensitic, PH or dual-phase stainless steels. Use at 3-5 V DC, 68°F [20°C], 5 seconds, stainless steel cathode. Ferrite outlines and colored tan. |
40mℓ water 60mℓ HNO3 | Electrolytic etch to reveal austenite boundaries but not twin boundaries in austenitic stainless steels (304, 316, etc.). Voltage is critical. Pt cathode preferred to stainless steel. Use at 1.4V DC, 2 minutes (see ref.2, pgs 235, 238 and 239). |
50mℓ Stock Solution* 1g K2S2O5 | Klemm's I Reagent. Immerse at room temperature until surface is colored. It is good to color ferrite in steel, reveals P segregation and overheating, etching time is 40-100 seconds. For coloring ferrite and martensite in cast iron low-alloy steels, usually up to 3 minutes. |
50mℓ Stock Solution* 5g K2S2O5 | Klemm's II Reagent. For steel sample, immerse for 30-90 seconds at 20°C, reveals P segregation. For austenitic Mn Steels, gamma yellow to brown or light to dark blue, alpha-martensite dark brown. Good for austenitic manganese steels. |
100mℓ Ehtanol 2mℓ HCl 0.5mℓ H2SeO4 | Beraha's Selenic Acid Etch 1. For cast iron, steels, and tool steels. For better result, Nital pre-etch is recommended. Use by immersion of sample until the sample surface is colored, usually up to 6 minutes. Cementite colored red-violet, ferrite colored yellow or brown, phosphide colored blue-green. |
100mℓ Ethanol 5-10mℓ HCl 1-3mℓ H2SeO4 | Beraha’s Selenic Acid Etch 2. In general, immerse sample at 20°C for 1-10 minutes. A yellow or light-brown surface color is formed to detect carbides and nitrides or an orange to red surface is formed to detect delta ferrite. Can use 20-30mℓ HCl for higher alloy grades, immersion time decrease with higher HCl. |
* Stock solution: aqueous cold-saturated Na2S2O3 solution |
Stainless Steel Imaging Tips
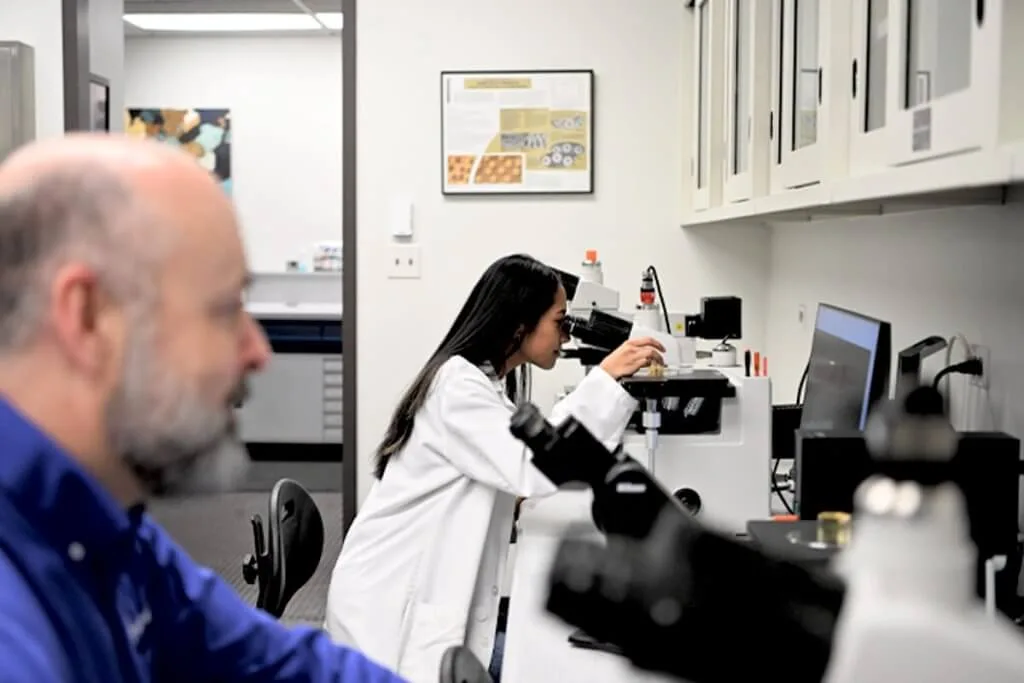
Depending on the alloy and application the goal of analysis can differ. Some common goals of the analysis are, contaminants, grain structure, phase percent, and dimensional measurements. Dimensional measurements can be taken and saved using one of the lower levels of our OmniMet® software. Though for other analysis and exporting needs more advanced versions of the OmniMet software maybe required.
Stainless Steel Hardness Testing Tips
Reference Materials for Hardness Testing | ||
---|---|---|
ASTM | ISO | |
Brinell | E10 | 6506 |
Rockwell | E18 | 6508 |
Vickers | E92,E384 | 6507 |
Knoop | E384 | 4545 |
Instrumented | E2546 | 14577 |
Conversions | E140 | 18265 |
ASM Handbook Volume 8: Mechanical Testing and Evaluation | Hardness Testing Section |
At Buehler, the equipment offered is made to perform at least one of the following scales: Brinell, Rockwell, Vickers and Knoop. If utilizing a scale previously mentioned there are standards for the method of testing. Standards such as the ones listed in the table are good places to reference the proper method of testing for the scales. Requirements for equipment, samples, testing methods and more are described within that can help determine the correct scale.
Equipment capabilities vary in levels of automation and documentation. Some pieces are integrated with hardness testing software. Software such as Buehler’s DiaMet can assist with testing parts more efficiently, accuracy and result documentation. This can be especially helpful when a large amount of indents must be done on one part.
Related Products
All Solutions by Material
Choose a material to view Buehler's resources
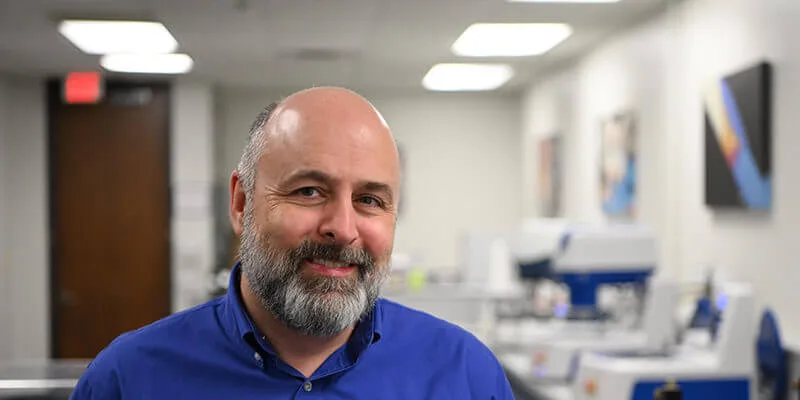
Find Your Solutions
Full Lab
Metallography Solutions
Do you want to improve your process? Reach out for one-on-one help from our applications experts.
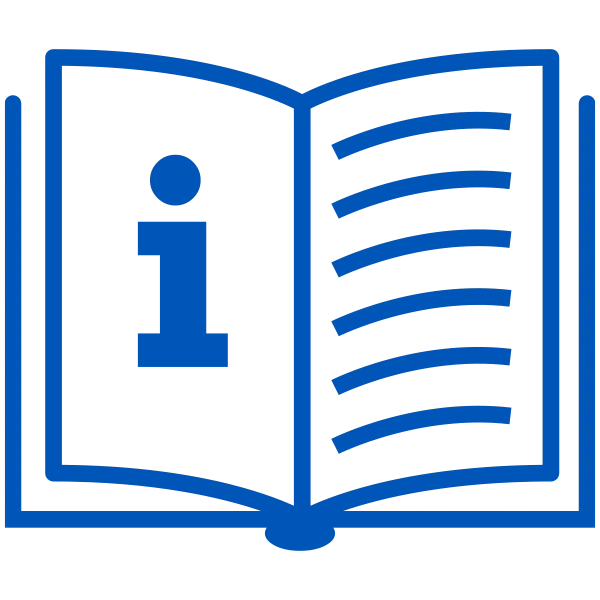
View all Products in the Buehler Product Catalog
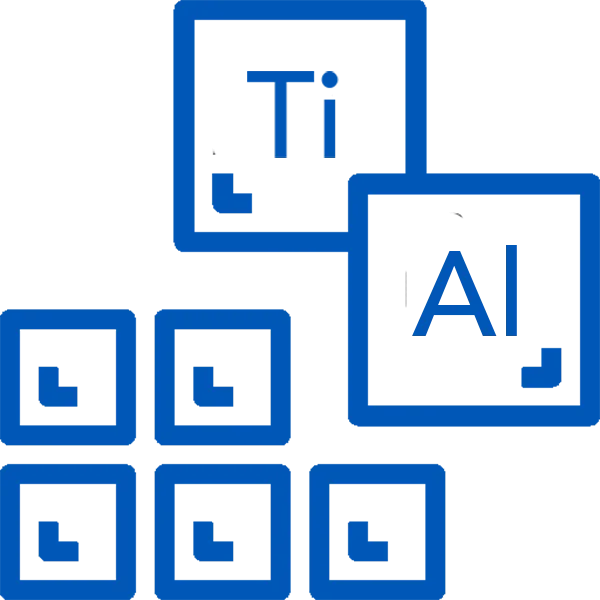
Select a method by material
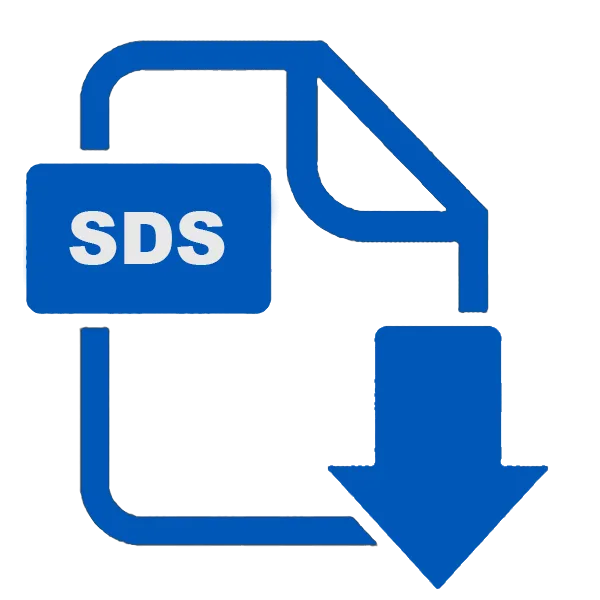
Search Buehler's Safety Data Sheets
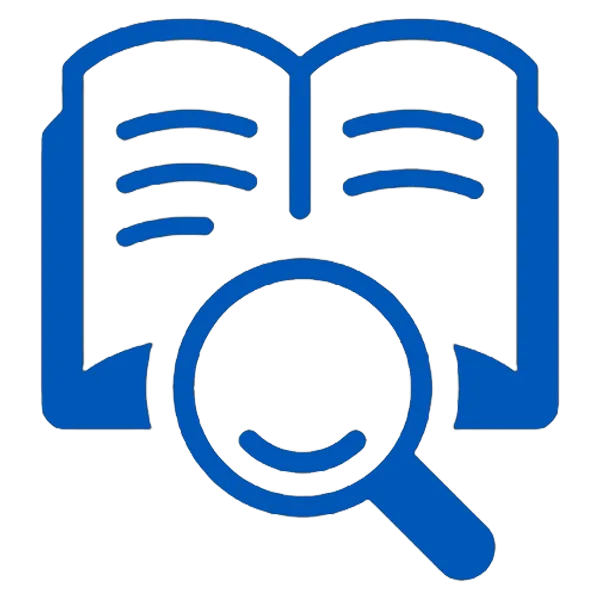
Browse and search Buehler's product literature