COMPONENTES ELECTRÓNICOS
Soluciones de preparación metalográfica por material
Utilice esta guía para saber por dónde empezar cuando realice la preparación metalográfica y el análisis de componentes electrónicos. Se incluyen consejos para obtener los mejores resultados en su aplicación metalográfica.
Aspectos a tener en cuenta al trabajar con componentes electrónicos

Dependiendo del material, hay ligeros cambios que pueden realizarse durante la preparación para mejorar el acabado superficial de las características deseadas. Por ejemplo, el silicio, el cobre y el FRP pueden requerir ajustes de proceso ligeramente diferentes para obtener resultados óptimos.
Consejos para el corte de componentes electrónicos

El seccionamiento agresivo puede causar daños mecánicos y térmicos, por lo que debe evitarse. Por este motivo, no se recomienda el corte abrasivo. El seccionado de precisión proporciona una excelente calidad de la superficie de corte y puede utilizarse para seccionar cerca de la zona objetivo.
Consejos para el corte de precisión

Los discos de precisión se utilizan en la preparación metalográfica de componentes electrónicos cuando se cortan muestras que son pequeñas o delicadas. Las discos de precisión no se rompen mientras se utilizan. En el borde exterior hay una sección en la que el abrasivo se ha unido con una aleación metálica y, si se cuida, pueden durar más que una caja de discos abrasivas. Los discos pueden utilizarse con cobre para cortes más difíciles, como realizar un corte preciso cerca de una característica de interés, o cuando es fundamental reducir la anchura de un corte (pérdida de kerf).
Otras ventajas de utilizar un disco de precisión son que se aplica una carga menor y, en consecuencia, se genera menos calor, lo que reduce la cantidad de daños.
Los discos abrasivos también se fabrican para las cortadoras de precisión. Se pueden utilizar en casos en los que el potencial de rotura de una disco es alto, como cuando una pieza es difícil de sujetar, es probable que se desplace durante el seccionado o existe una gran variabilidad en el proceso (por ejemplo, varios operarios).
Discos de precisión recomendadas para componentes electrónicos | ||||
---|---|---|---|---|
Material | 127 mm (5 in) | 178 mm (7 in) | 203 mm (8 in) | Piedra de limpieza |
Silicio | 11-4255 0,4 mm [0,015 pulg.] | 11-4277 0,6 mm [0,024 pulg.] | 11-479 1,1 mm [0,045 pulg.] |
11-1190
11-2490 |
Otros componentes electrónicos | 11-4255 0,4 mm [0,015 pulg.] | 11-4247 0,6 mm [0,024 pulg.] | 11-4248 0,9 mm [0,035 pulg] |
11-1190
11-2490 |
Consejos de montaje para componentes electrónicos

El montaje de muestras metalográficas puede permitir la automatización y aumentar la facilidad de manipulación durante los pasos posteriores de la preparación y el examen metalográficos. Las muestras de formas intrincadas pueden montarse para crear formas uniformes que permitan la automatización del proceso de preparación de la muestra.
El montaje de las muestras también protege y preserva los bordes o defectos superficiales durante la preparación metalográfica. El método de montaje no debe alterar en modo alguno la microestructura de la muestra. La presión y el calor son las fuentes más comunes de efectos perjudiciales. Las temperaturas en torno a 350oF y las presiones en torno a 4000 PSI son comunes para el montaje por compresión en caliente.
La geometría y las propiedades de la muestra pueden determinar el método adecuado para el montaje de componentes electrónicos. Se recomienda un sistema epoxi de baja viscosidad y buena calidad, como EpoxiCure® o Epo-Thin®.
Una selección cuidadosa puede garantizar que el material satisface las necesidades de montaje en cuanto a tiempo, viscosidad, temperatura y contracción. Los sistemas acrílicos pueden aumentar el rendimiento con tiempos de curado rápidos de entre 5 y 30 minutos. Sin embargo, los sistemas acrílicos no se recomiendan debido a sus bajos niveles de adhesión e infiltración de la muestra. Los sistemas epoxídicos son los medios de montaje recomendados para los componentes electrónicos. Con viscosidades más bajas y tiempos de trabajo más largos, el epoxi mezclado puede utilizarse con un sistema de vacío para ayudar a los niveles de penetración en geometrías intrincadas.
Estas pequeñas características y geometrías intrincadas pueden dificultar la infiltración. Una infiltración incompleta puede dar lugar a poros que pueden complicar el análisis dando lugar a errores en la medición. Cuando se trabaja con EpoxiCure o EpoThin, calentar la resina a 40oC en un horno antes de mezclarla puede reducir la viscosidad y aumentar la infiltración. Verter bajo un vacío de 22-24 inHg y ciclar las muestras bajo vacío varias veces en intervalos cortos de tiempo, aproximadamente 60 segundos, también puede ayudar a la infiltración de los sistemas epoxi. Este ciclo puede automatizarse utilizando el sistema de vacío SimpliVac.
Consejos de desbaste y pulido de componentes electrónicos para todos los métodos

Cuando los componentes electrónicos contienen metales no ferrosos y polímeros que son el centro de atención, el paso final de pulido completado debe ser un paso MasterPrep®. La alúmina también es mejor cuando se analizan materiales no reactivos como el níquel y el oro.
Si se analiza silicio, el desbaste debe comenzar con un tamaño de abrasivo no superior a 600 granos. Debido a su naturaleza dura y quebradiza, el uso de un abrasivo de grano superior a 600 puede provocar importantes daños por impacto. La suspensión de sílice coloidal, como MasterMet®, es más adecuada para los materiales de silicio y debe utilizarse para el paso final del procedimiento de pulido.
Otros materiales para los que la sílice coloidal también es más adecuada son muestras como el vidrio, los óxidos, el aluminio y el cobre. Si el objetivo es el análisis de interfase, el diamante fino para los pasos finales del pulido puede proporcionar claridad sobre los óxidos.
Cuando la soldadura de plomo eutéctica o casi eutéctica es de interés, se puede utilizar el método general siguiente con un ligero cambio. En lugar de suspensión de diamante, debe utilizarse pasta para reducir las posibilidades de incrustación de abrasivos.
El uso del sistema de dosificación Burst de Buehler puede conservar los diamantes y mejorar la consistencia.
La tasa ideal para el sistema de dispensación Burst cambia con el tamaño de la platina y el paño de pulido que se está utilizando. Como pauta general, para el tamaño de la plato de 8″ un ajuste de ráfaga de 3 es un buen punto de partida, para tamaños de 10″ y 12″ ajuste el sistema de ráfaga a 4 y ajuste según sea necesario. Es posible que sea necesario experimentar un poco para determinar los ajustes óptimos que garanticen un abrasivo y una humectación del paño suficientes. Los dosificadores de ráfaga también son capaces de dosificar extendedores simultáneamente con el diamante, si se desea.

Las cargas indicadas en los métodos de desbaste y pulido son recomendaciones para una muestra montada de 1,25″. Si se utiliza la fuerza central durante la preparación, la fuerza indicada debe multiplicarse por el número de muestras que se pulen. Para diferentes tamaños de muestra, utilice nuestra calculadora de conversión de carga para determinar la carga correcta para su aplicación.
Método para componentes electrónicos en general | ||||
---|---|---|---|---|
Superficie | Cargas [N] | Velocidad Base [rpm] | Rotación Relativa | Tiempo |
CarbiMet® grano 320 | 3 [13] | 150 rpm |
![]() | Hit edge of target |
TextMet® P con 9um MetaDi® Supreme Diamond | 5 [22] | 150 rpm |
![]() | 5:00 |
VerduTex con 3um MetaDi Supreme Diamond | 5 [22] | 150 rpm |
![]() | 3:00 |
VerduTex con 1um MetaDi Supreme Diamond | 5 [22] | 150 rpm |
![]() | 3:00 |
ChemoMet® con 0.05um MasterPrep® Alumina | 3 [13] | 150 rpm |
![]() | 1:30 |
![]() ![]() |
Método de preparación del silicio en dispositivos microelectrónicos | ||||
---|---|---|---|---|
Superficie | Cargas [N] | Velocidad Base [rpm] | Rotación Relativa | Tiempo |
CarbiMet® grano 600 | 3 [13] | 100 rpm |
![]() | Until Plane |
VerduTex con 6um MetaDi Supreme Diamond | 5 [22] | 100 rpm |
![]() | 3:00 |
VerduTex con 3um MetaDi Supreme Diamond | 5 [22] | 100 rpm |
![]() | 3:00 |
VerduTex con 1um MetaDi Supreme Diamond | 5 [22] | 100 rpm |
![]() | 3:00 |
ChemoMet® con 0.06um MasterMet® Colloidal Silica | 2 [9] | 100 rpm |
![]() | 2:00 |
![]() ![]() |
Consejos para el grabado de componentes electrónicos

Componentes electrónicos

Los componentes electrónicos pueden ser analizados para medir una variedad de cosas dependiendo de la composición y aplicación. Algunos objetivos comunes del análisis son las mediciones de características o defectos, como huecos, grietas, retrograbados y contaminantes. Las mediciones dimensionales pueden tomarse y guardarse utilizando nuestro software OmniMet® Basic. Para otras necesidades de análisis y exportación, pueden ser necesarias versiones más avanzadas del software OmniMet.
Consejos para el ensayo de dureza de componentes electrónicos

Materiales de referencia para ensayos de dureza | ||
---|---|---|
ASTM | ISO | |
Brinell | E10 | 6506 |
Rockwell | E18 | 6508 |
Vickers | E92,E384 | 6507 |
Knoop | E384 | 4545 |
Instrumentación | E2546 | 14577 |
Conversiones | E140 | 18265 |
Manual ASM Volumen 8: Ensayos Mecánicos y Evaluación | Sección de ensayos de dureza |
Cuando se está determinando el método de ensayo de dureza, se evalúa la aplicación para encontrar la escala que satisfaga todas las necesidades y normas. En Buehler, nuestro equipo soporta pruebas de dureza utilizando cuatro escalas: Brinell, Rockwell, Vickers y Knoop. Dependiendo de la información requerida y de los estándares a cumplir, la escala requerida puede cambiar. En la tabla de al lado se enumeran varios buenos materiales de referencia para los métodos de ensayo. En el caso de los componentes electrónicos de menor tamaño, son habituales los ensayos Vickers y Knoop.
El acabado de la superficie de la probeta; la planitud y los rasguños podrían dificultar las muescas de automedición del software. Para reducir el acabado desigual de la superficie, asegúrese de que las muestras estén planas antes de iniciar el proceso de pulido.
El ensayo de componentes electrónicos puede resultar difícil debido a las diferencias de reflectancia entre los componentes. Un buen contraste es importante a la hora de realizar mediciones de sangría. Puede ser necesario ajustar la iluminación para cada componente. Algunos programas informáticos de ensayo de dureza, como DiaMet Full-automatic, disponen de ajustes que permiten automatizar la iluminación y el enfoque para cada sangría realizada.
Las puntas de indentación pueden quedar ocultas u oscurecidas dentro de poros y grietas. Los componentes cerámicos son especialmente susceptibles a esto. Una forma de mitigar estos efectos es utilizar una carga más ligera. Las cargas más ligeras no sólo reducen las posibilidades de que se produzcan grietas, sino que también permiten centrarse en zonas más pequeñas del material. Configure el equipo con un objetivo de 100 aumentos cuando mida hendiduras de 20 micras o menos. El aire atrapado en la resina utilizada para el montaje podría formar poros. Deben evitarse los poros durante los ensayos.
Los niveles de automatización y documentación se basan en la escala utilizada. Si se necesita automatización, se deben discutir los diferentes niveles de DiaMet disponibles con un comprobador. La automatización de los procesos de ensayo puede ayudar a aumentar el rendimiento de los sistemas de análisis y la repetibilidad.
Productos relacionados
Todas las soluciones por material
Elija un material para ver los recursos de Buehler
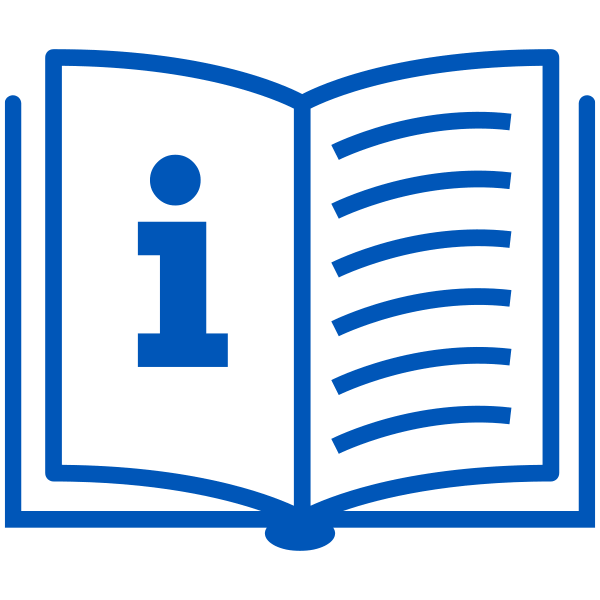
Ver todos los Productos del Catalogo de Productos Buehler
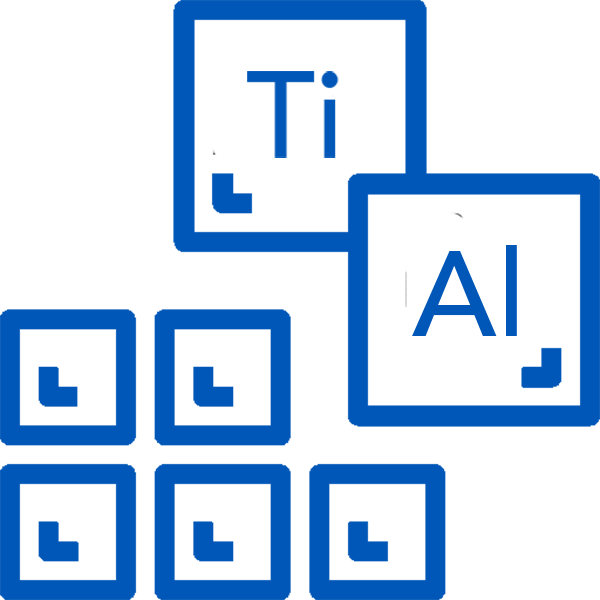
Seleccione un método por material
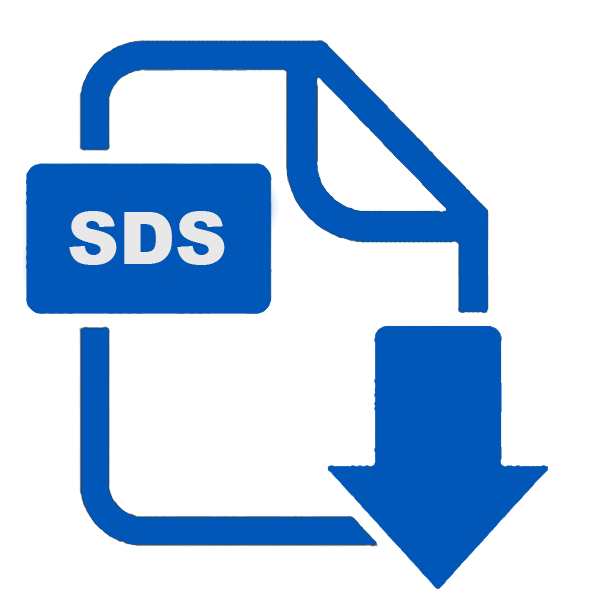
Buscar las hojas de datos de seguridad de Buehelr
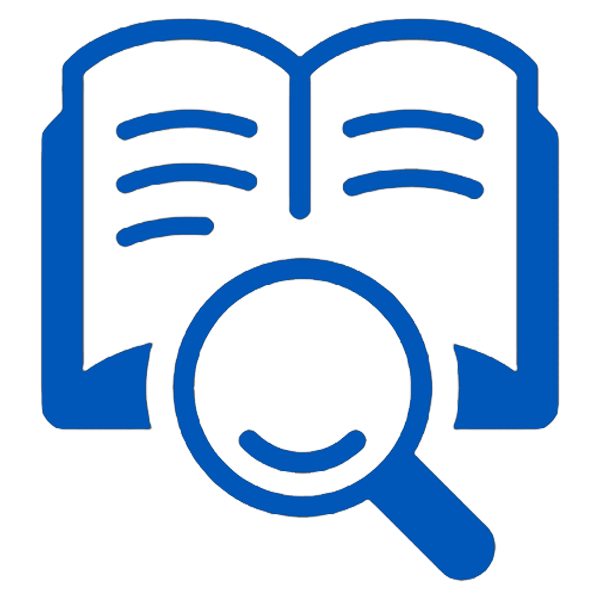
Examinar y buscar literatura de productos de Buehler